本記事で分かること
部品実装方法(リフロー、フロー)がどんな方法で、どのような場合に使用するかわかる。
半田付けは、フロー方式、リフロー方式、手づけ方式の3つがあります。
ここでは、フローとリフローの概要と、その違いについて説明します。
フロー、リフローの概要 と 違いについて
2つの方法の概要は次の通りです。
・フロー方式:溶かした半田を、半田付けする部分に当てて接合する。
主にリード部品の半田付けに使用。
チップ部品も使用できるが、フロー対応品に限る。
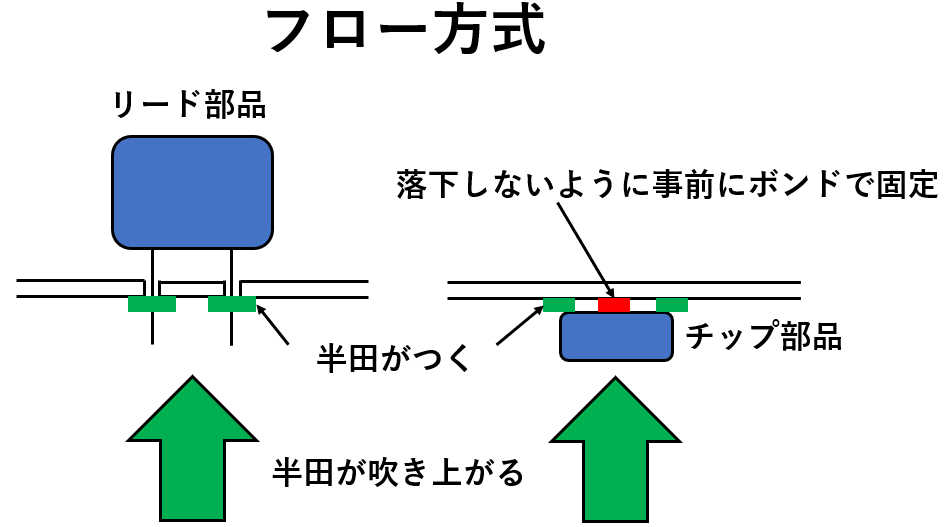
・リフロー方式:クリーム半田を、半田付けする部分に塗ってから熱で溶かして接合する。
チップ部品の半田付けに使用。
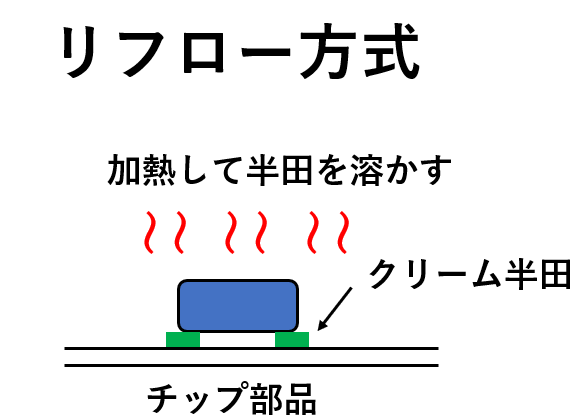
2つの違いは、
最初から溶けた半田を部品につける(フロー)、
溶けてない半田の上に部品を載せて、加熱して半田を溶かす(リフロー)、
になります。
次にフロー、リフローの長所と短所について説明します。
フロー半田の長所と短所
<長所>
・リード部品の半田付けは、手づけ以外はこの方法のみ。
・半田面のチップ部品も、部品面に搭載したリード部品と同時に半田付けできる。
(但し、チップ部品が落ちないように、事前にボンドで固定しておく)

<短所>
・半田付け不良が起こりやすい
部品の高さや配置によって全部品に同様に半田を当てる事が難しい為、
半田ショートや未半田となる場合がある。
(基板設計時に部品配置やパターンを配慮することで減少させことができる)
・小さいチップ部品の実装に不向き
1608(1.6mm×0.8mm)サイズが限界。
それ以下は、チップの脱落や半田ショートの可能性が高くなる。
部品メーカーでフロー対象外としているものがほとんど。
・フロー不可のチップ部品が多い
リフローに比べ、加熱温度が高く、直接半田を部品に吹き付けるため、
耐熱性等の理由で部品メーカーがフロー禁止にしている場合がある。
次にフロー半田工程について説明します。
フロー半田の流れ
表面(部品面)をリード部品、裏面(半田面)はチップ部品を実装する場合で説明します。
1.ボンド塗布
チップ部品が落ちないように固定するため、部品搭載位置にボンドをつける。
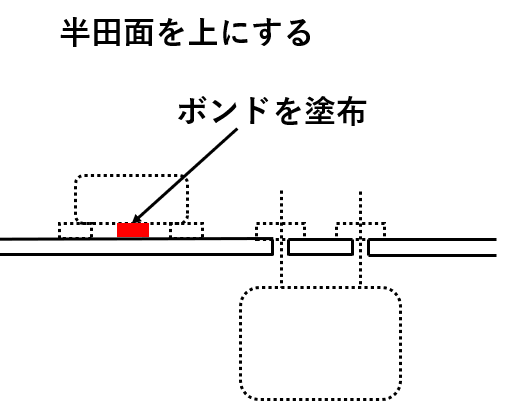
2.チップ部品を搭載
ボンドをつけた箇所に部品を搭載する。
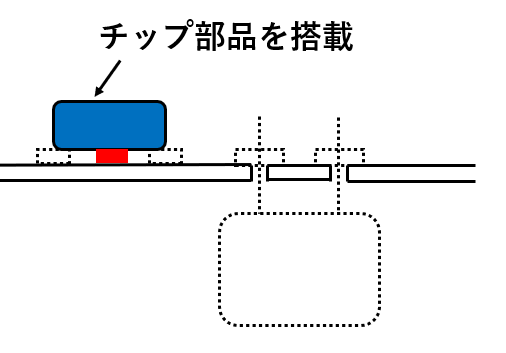
3.ボンド硬化
フロー炉(又はリフロー炉)で加熱することでボンドが硬化し、部品が固定される。
(90~150℃加熱で1~2分で硬化)

4.リード部品を搭載
リード部品を基板に挿入する。機械挿入できない部品は手で挿入する。
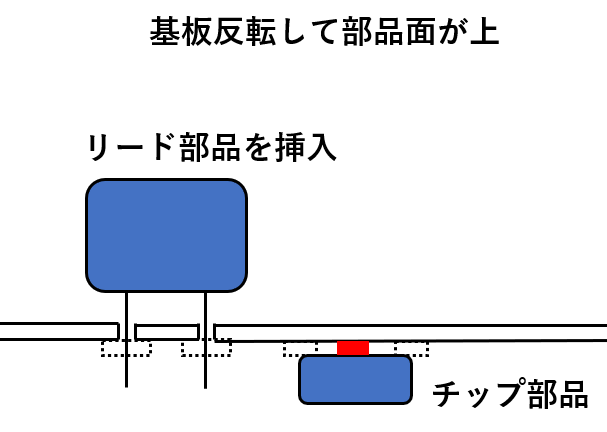
5.半田面をフラックス塗布
フラックスにより、基板のパッド、ランドの金属表面を清浄し,半田をつきやすくする。
(パッド、ランドについては基板の部位名称についてを参照)
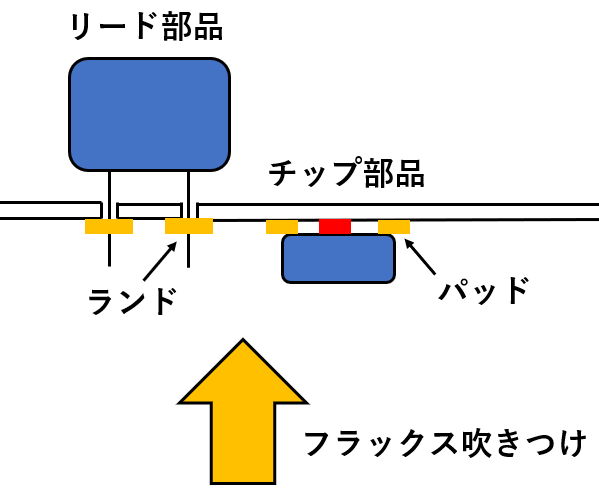
6.フロー炉で半田付け
チップ部品を搭載した面(半田面)を下にして、半田を吹き上げて半田付けする。
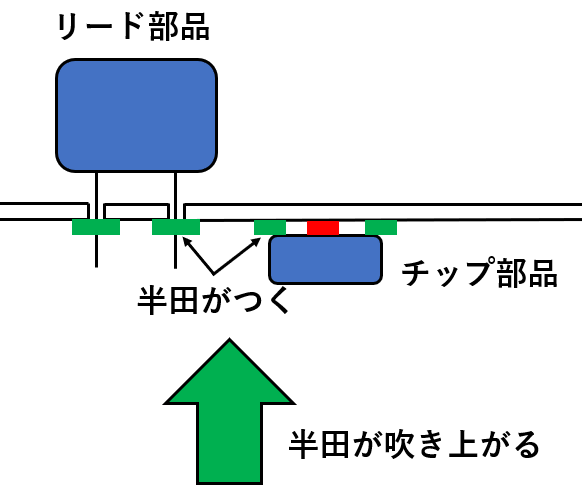
フロー半田については以上です。
次にリフローについて説明します。
リフロー半田の長所と短所
<長所>
・チップ部品の実装に最適
フローと違い、チップ部品でリフロー禁止の部品はない。
(というより、これ以外に実装方法がない)
・半田付け不良が起こりにくい
最初から半田付けする部分に適切な量の半田をつけるので、半田ショートや未半田が起こりくい。
<短所>
・リード部品が実装できない
チップ部品と違い、半田をつける前に部品を挿入しなくてはならず、
基板上に部品が搭載された状態では、クリーム半田を印刷できないため。
・メタルマスクが必要
クリーム半田を印刷するのに必要な板(詳細は後で説明)。
半田付けする面ごとに必要で、両面リフローの場合は2枚制作する。
基板のパターン(部品配置)を変更したら、作り直す必要がある。
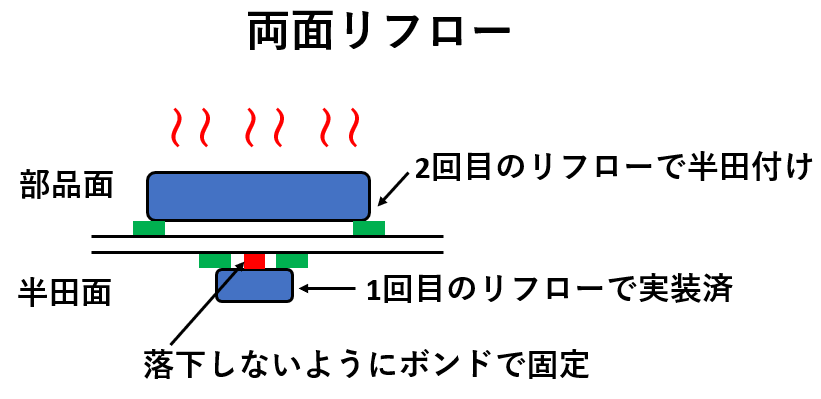
次にリフロー半田工程について説明します。
以下の記事で、基板工作で役立つ工具類を紹介しています。
リフロー半田の流れ
基板の両面(部品面、半田面)にチップ部品を実装する場合(両面リフロー)で説明します。
1回目のリフローは小さいチップを搭載することが多い半田面にする。
部品面は重量のある大型部品(CPUやメモリなど)が搭載されることが多く、
先に実装すると、半田面のリフロー時に熱で半田が溶けた時、落下する危険が高い。
<リフロー1回目 半田面>
1.クリームはんだを印刷
クリーム半田と呼ばれるペースト状の半田をメタルマスクを用いて必要な箇所に印刷する。
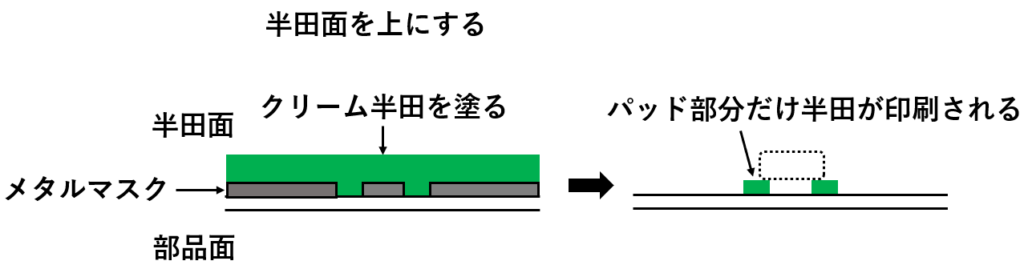
メタルマスク
クリーム半田を印刷する箇所(基板上のパッド部分)だけ穴の開いた板。
基板の上に重ねてからクリーム半田を塗ることで、半田がパッドだけに付着する。
基板設計時に作成されるガーバーデータを元に製作される。
半田付けする面ごとに1枚必要で、両面リフローの場合は2枚必要となる。
メタルマスクは基板実装メーカが製作、保管することが多いので、回路設計者は目にすることが少ないかもしれません。
2.ボンド塗布
基板のチップ部品搭載位置にボンドをつける。
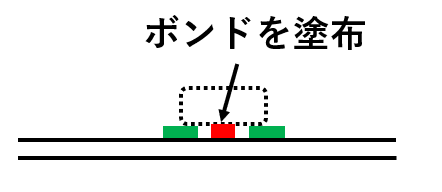
両面リフロー時は初回のリフロー実装部品をボンドで固定することで、
反対面のリフロー時に、熱で半田が溶けて部品が落下しないようにする。
3.チップ部品を搭載
クリーム半田&ボンドをつけた箇所に部品を搭載する。
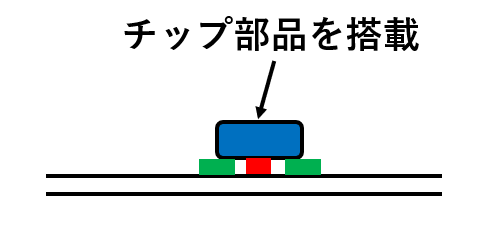
4.リフロー炉で半田付け
炉で加熱することで、クリーム半田を溶かし、ボンドを硬化させて部品を半田付けする。
ボンドの硬化温度(約130℃)よりクリーム半田の溶融温度(約230℃)の方が高いので、
半田の温度に合わせれば、ボンドも硬化する。
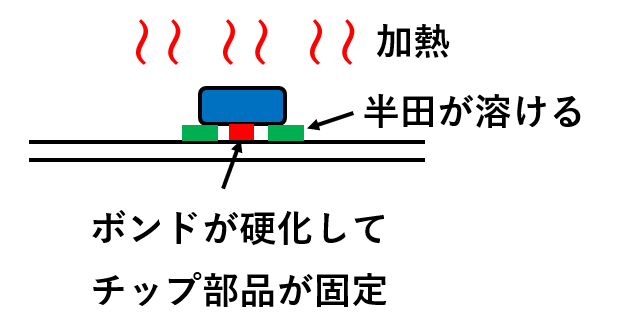
<リフロー2回目 部品面>
5.クリームはんだを印刷
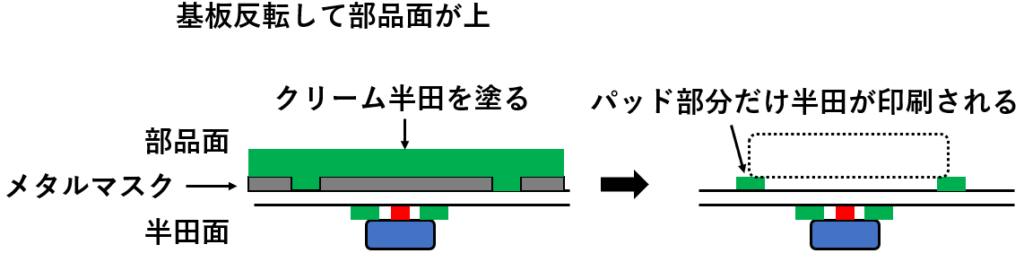
6.チップ部品を搭載
ボンド塗布は不要:下向きで加熱しないので、落下する心配がないため。
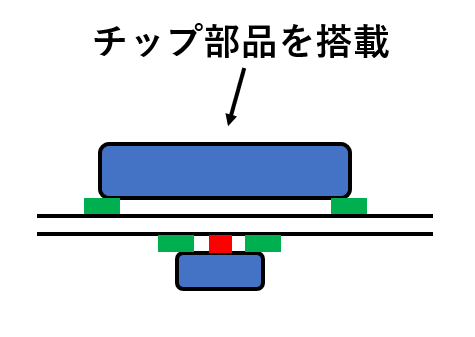
7.リフロー炉で半田付け
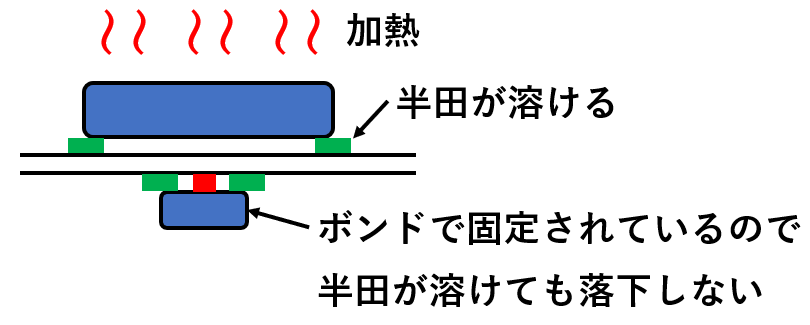
リフローについては以上です。
最後に、フロー、リフローを両方行う場合について説明します。
フローとリフローの順番は?
基本的にリフロー→フローの順で行われます。
理由は、基板上に部品が搭載された状態では、クリーム半田を印刷できないためです。
基板の裏表に搭載する部品がDIPかSMDによって、実装は次のような手順になります。
(これ以外の手順も存在します)
DIP(Dual-in-line package) :リード部品
SMD(Surface Mount Device):チップ部品
・片面(DIP部品のみ)の場合
フロー
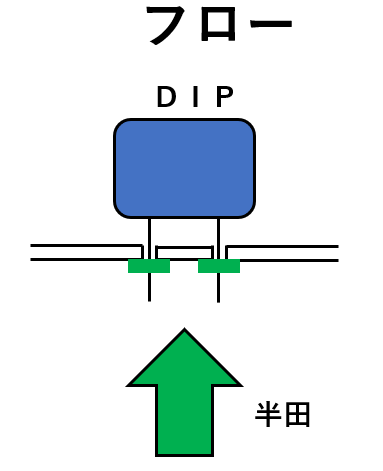
・両面(表面:DIP 裏面:SMD)の場合
フロー又は、リフロー+フロー(※半田パレットが必要)
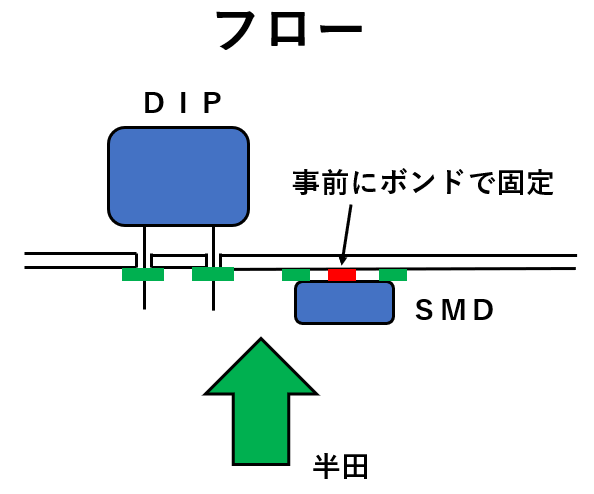
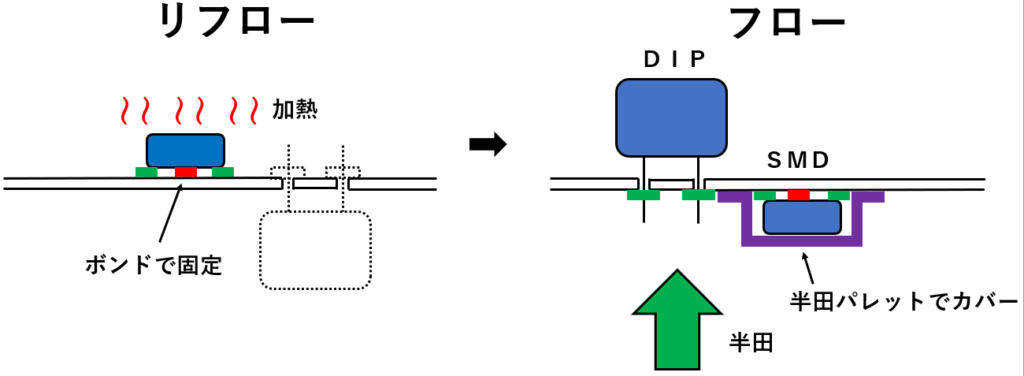
※半田パレット(ディップパレット、ソルダーパレット)
リフロー実装済の部品の部分だけマスクし、フロー半田が当たらないようにした板。
マスク部分への熱を遮断し、リフロー実装済の半田を溶かさないようにする。
・両面(表面:DIP+SMD 裏面:SMD)の場合
表面SMDリフロー+DIPと裏面SMDフロー
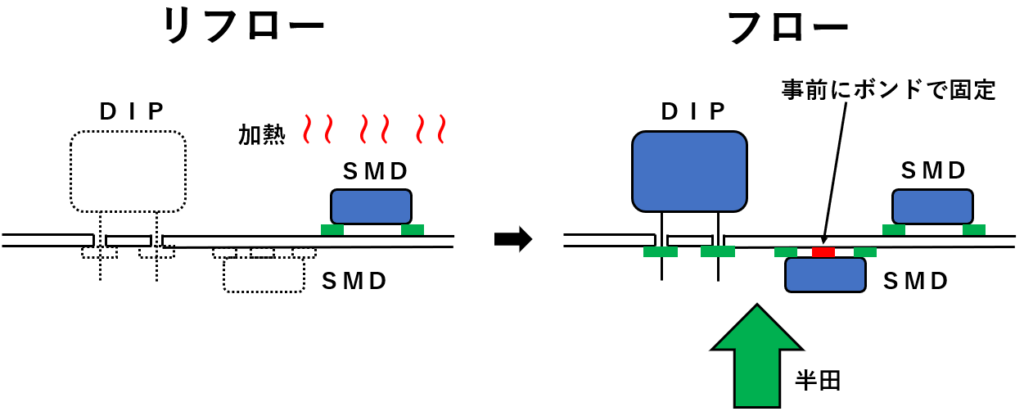
・両面(表裏ともSMD)の場合
リフロー(ボンド固定)+リフロー
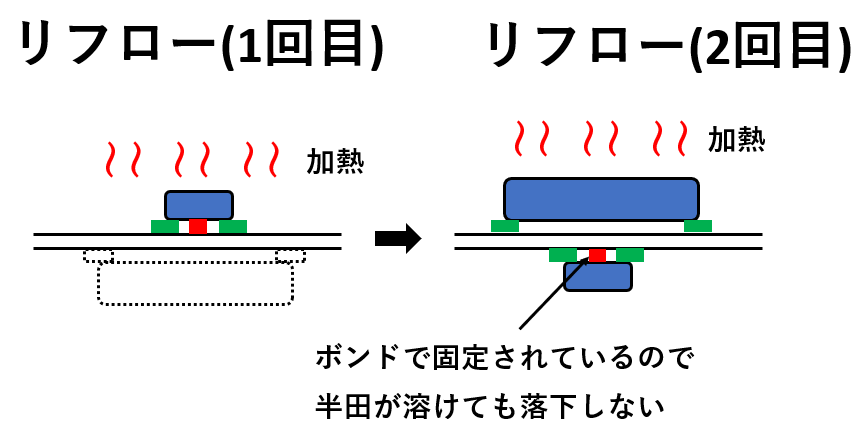
フロー、リフローの特徴を考慮した回路・基板設計をすることで、
実装不良が少なく、コストも低い基板を制作することができます。
次回は、実装を考慮した回路・基板設計方法について説明します。
<パターン幅、間隔の決め方について解説しています>
以下の記事で、基板工作で役立つ工具類を紹介しています。
<トランジスタのベース抵抗の決め方等、トランジスタの基本設計について解説しています>
<エミッションやイミュニティなどEMC試験方法について、分かりやすく解説しています>