この記事でわかること
・同じ抵抗シリーズでも、抵抗値によって定格電圧は異なる
・データシートの定格電力をそのまま使用してはいけない
・ディレーティングをとっても、基板が熱に耐えられない場合がある
電子部品を選ぶ際は、
回路で発生する電圧や電流よりも
部品の定格が十分大きいものを選定します。
どの程度大きくするか余裕度を表すのがディレーティングです。
一般的なディレーティングの目安としては、以下になります。
損失: 定格の50%以下
電圧、電流、温度 : 定格の80%以下
しかし、チップ抵抗については、
この基準だけで選定すると痛い目にあうかもしれません。
その理由は発熱の殆どがプリント基板に伝わる為、
抵抗の耐熱は問題なくても、基板が耐えられないからです。
また、基板の熱は周囲の部品にも伝わります。
電解コンデンサは高温になると寿命が短くなります。
また、チップ抵抗同士も、お互いの熱を受け取るので、
密集して実装すると、自己発熱以上の温度になり、故障する恐れがあります。
ここでは、チップ抵抗のディレーティングの決め方について解説します。
チップ抵抗に印加できる電圧を求める
チップ抵抗のディレーティングを決める手順について、
KOA製2012サイズの標準抵抗RK73B2A 抵抗値10kΩを例にして説明します。
この抵抗の最高使用電圧は150Vで、定格電力が0.25Wです。
先程述べたように、電圧ディレーティングの目安は定格電圧の80%ですが、
ここで、データシートの最高使用電圧をそのまま定格電圧として適用してはいけません。
(定格電力×公称抵抗値)0.5 を計算し、
その値が最高使用電圧よりも低ければ、そちらを定格電圧とします。
抵抗値10kΩでは、
(定格電力×公称抵抗値)0.5 = (0.25×10k)0.5=50V
最高使用電圧は150Vですが、電圧の低い計算値50Vが定格電圧になります。
ちなみに、抵抗値100kΩの場合は、
(定格電力×公称抵抗値)0.5 = (0.25×100k)0.5=158V
最高使用電圧150Vを超える事はできないので、定格電圧は150Vになります。
抵抗値による定格電圧の変化を下図に示します。
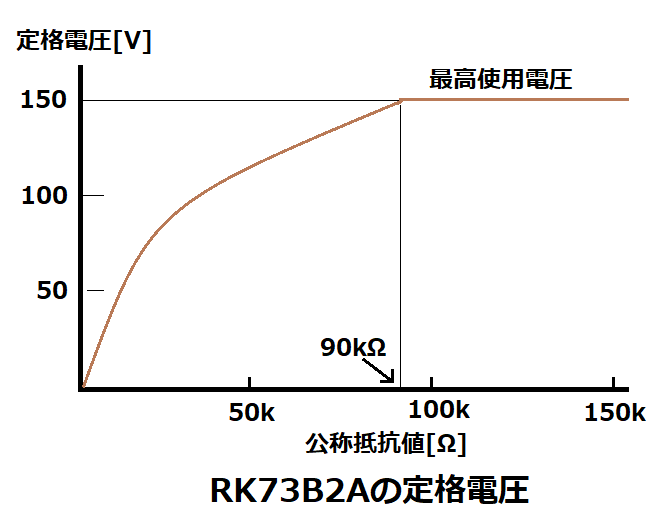
この図より、この抵抗は90kΩ以下で定格電圧が下がることが分かります。
このように、同じシリーズのチップ抵抗でも
抵抗値によって定格電圧が変わるので注意して下さい。
今回の例では、定格電圧は50Vなので、
この抵抗に印加できる電圧は、定格電圧の80%より、
50V×0.8=40V
となります。
チップ抵抗で消費できる電力を求める
消費電力については、ディレーティングの目安は定格電力の50%以下にします。
但し、定格電力についても、データシートの定格電力をそのまま適用してはいけません。
データシート記載の定格電力は端子部温度が定格以下という前提で決められた値です。
(下記コラム参照)
しかし、設計段階では実際の回路が無く、端子部温度を測定できないので、
データシートにある周囲温度を基準にした負荷軽減曲線を使用して、定格電力を求めます。

この時の周囲温度ですが、設計する製品の周囲温度では無く、
チップ抵抗の周囲温度であることに注意して下さい。
ここでは、チップ抵抗の周囲温度の目安として、100℃にします。
理由は、これ以上発熱すると、基板が損傷するからです。
一般的なプリント基板であるFR-4の耐熱温度は120℃なので、
それ以上の温度になると、チップ抵抗は問題なくても基板が持ちません。
チップ抵抗は部品表面から放熱することが殆どできません。
チップ抵抗の発熱のうち、部品表面から放熱する割合は、
大型の6432サイズですら5%で、2012だと僅か1%です。
このため、チップ抵抗の熱の殆どが端子部から基板に伝わります。
従って、基板はチップ抵抗の放熱板と考えるのが適切です。
データシートの負荷軽減曲線より、
周囲温度100℃時の定格電力比は65%なので、
定格電力は、
0.25W ×0.65=0.16W
となります。
以上から、この抵抗に印加できる電力は、
ディレーティングを50%すると、
0.16 × 0.5=0.08W
となります。
コラム:チップ抵抗の定格電力がアップしていた?
20年以上、設計をしている人なら、気づいている方もいると思いますが、
2000年以降、3216サイズ以下のチップ抵抗器の定格電力が倍増しています。
KOA テクニカルノート「表面実装抵抗器の負荷軽減」より
しかし、これは抵抗器の性能が上がった訳ではありません。
定格電力の評価を周囲温度でなく、端子部温度を基準にして再評価を行った為です。
負荷軽減曲線を見てもわかるように、端子部温度を基準にした場合、
より高い温度まで定格電力を維持できることがわかります。
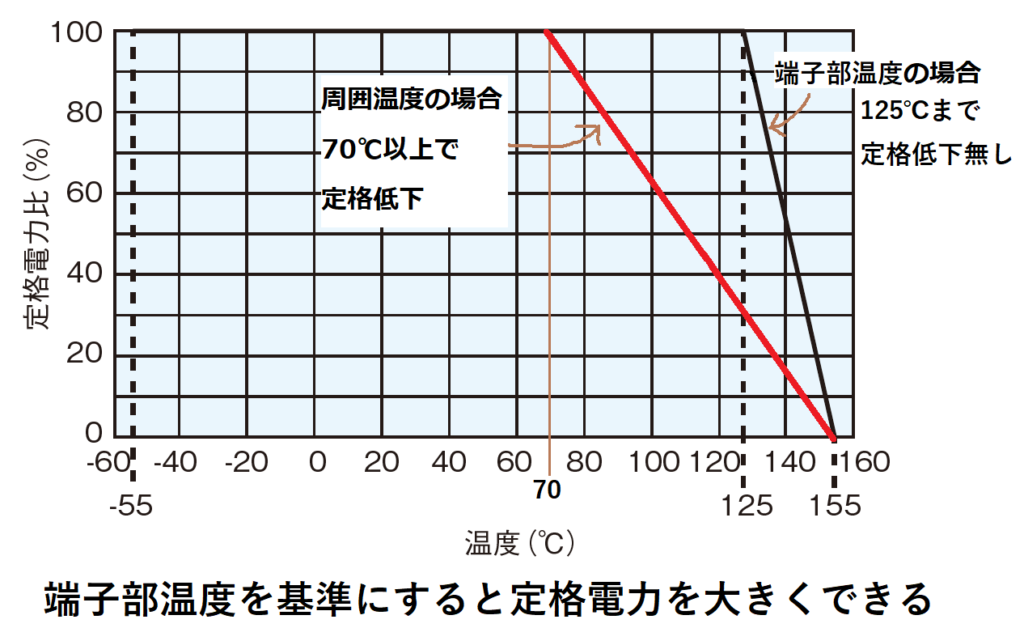
これは基板のパターン幅や、周りの部品からの発熱に
大きく影響されることを意味します。
このため、端子部温度を測定できない設計段階において、
データシートの定格電力をそのまま使うのは危険です。
従って、先程解説した周囲温度の負荷軽減曲線から
定格電力を算出する必要があるのです。
チップ抵抗を密集させた時、基板温度に注意
抵抗の消費電力が大きい場合や、耐圧を確保するため、
チップ抵抗を複数個接続する場合は温度に注意する必要があります。
チップ抵抗が密集すると、隣の抵抗からの熱も伝わり、
自己発熱以上の温度になります。
この場合、定格電力の50%以下で使用しても、
基板温度が100℃を超える恐れが出てきます。
また、ここまで基板温度が上昇しなくても、
近くに電解コンデンサがあると寿命を縮めてしまいます。
アレニウスの法則より、
電解コンデンサは10 ℃上昇すると、寿命が半分になります。
電解コンデンサは電子部品の中で最も寿命が短いので、
設計する製品そのものの寿命が短くなってしまいます。
電界コンデンサの寿命については下記記事で解説しています。
実際に温度測定を行った結果を紹介します。
測定するチップ抵抗は、KOA製 WK73R2Bです。
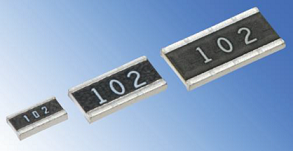
この抵抗は長辺電極型で、端子部が長い形状でその分、放熱しやすくなっており、
3216サイズながら定格電力0.75Wと高電力タイプとなっています。
先程解説した印加電力の求め方より、
負荷軽減曲線を用いて、周囲温度100℃における定格電力比は65%なので、
定格電力は
0.75W×0.65=0.49W
になります。
印加できる電力は、ディレーティングを50%とすると、
0.49W×0.5=0.25W
になります。
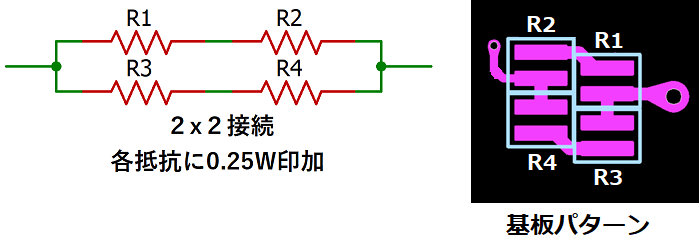
この抵抗を印加電力0.25Wで、図のように2×2接続した時、
室温25℃、1分間で、チップ抵抗の温度は117℃になりました。

この抵抗4個の印加電力の合計は0.25W×4=1Wです。
わずか1Wで、これだけの温度になります。
定格電力の半分で使用しても、チップ抵抗を密集すると
基板が持たない恐れがあることがわかります。
対策としては、以下になります。
・抵抗の間隔を空ける
但し、間隔をチップ抵抗1個程度広げただけでは殆ど効果が無いです。
また、パターン幅を広げる方法もありますが、
これも数倍広げただけでは、やはり効果は小さいです。
・抵抗の数を増やす
1個当たりの印加電力を更に下げる方法です。
消費電力にもよりますが、抵抗数を2倍以上増やさないと効果がありません。
・リード抵抗にする
これが一番確実な方法です。
基板から浮かして実装することで基板に熱が伝わりにくくなります。
チップ抵抗を倍増して実装面積が増えるくらいなら、
リード抵抗の方がコンパクトになる事が多いです。
<以下の記事で、基板の部品交換や修正で役立つ工具類を紹介しています>